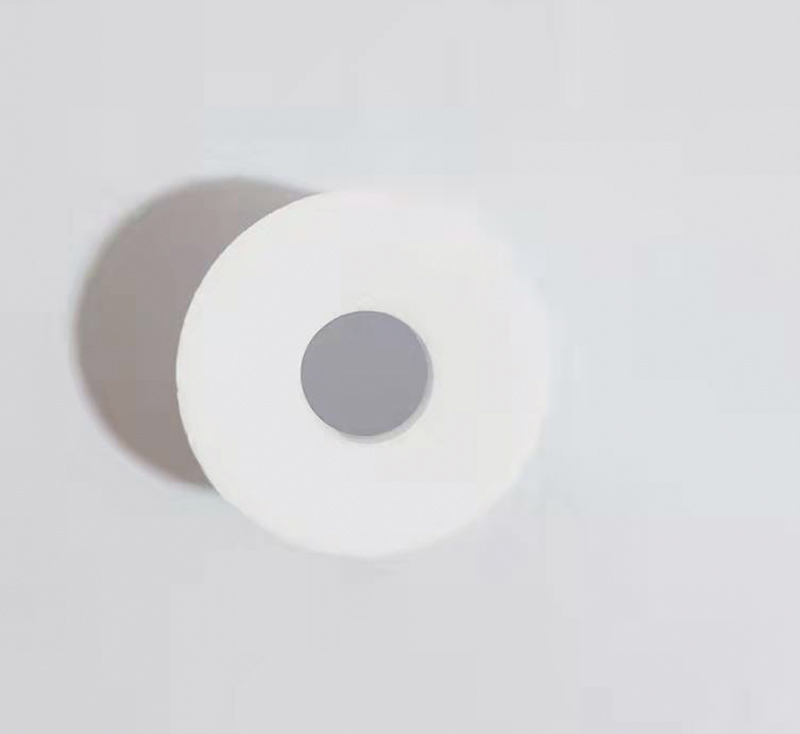
Design Developing New Model Plastic Injection Molding Parts
Material:PS, ABS, PP, PVC, PMMA, PBT, PC, POM, PA66, PA6, PBT+GF, PC/ABS, PEEK, HDPE, TPU, PET, PPO,...etc.
Application:Medical, Household, Electronics, Automotive, Agricultural
Shaping Mode:Plastic Injection Mould
Consult
Product Details:
Fast production and highly efficient | Injection moulding can produce an incredible amount of parts per hour. Speed depends on the complexity and size of the mould. |
Low labour costs | Plastic injection moulding is an automated process whereby a majority of the process is performed by machines and robotics, which a sole operator can control and manage. Automation helps to reduce manufacturing costs, as the overheads are significantly reduced. |
Design flexibility | The moulds themselves are subjected to extremely high pressure. As a result, the plastic within the moulds is pressed harder and allows for a large amount of detail to be imprinted onto the part and for complex or intricate shapes to be manufactured. |
High-output production | Thousands of parts can be produced before the tooling needs to be maintained. |
Product consistency |
Injection Moulding is a repeatable process; in other words, the second part you produce is going to be identical to the first one etc. This is a huge advantage when trying to produce high tolerances and part reliability in high volumes. |
Low scrap rates | Injection moulding produces very little post-production scrap relative to traditional manufacturing processes. Any waste plastic typically comes from the sprue and runners. Any unused or waste plastic, however, can be reground and recycled for future use. |